Lohmann & Rauscher
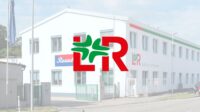
Lohmann & Rauscher (L&R) is a leading international developer, manufacturer and supplier of high-quality, future-oriented medical devices and hygiene products – ranging from conventional bandages to modern treatment and nursing systems. Created in 1998 from the merger of the two companies Lohmann (founded in 1851) and Rauscher (founded in 1899), L&R has 170 years of expertise as a dependable partner and solution provider for its customers.
With 5,400 employees, 50 subsidiaries and shareholdings, as well as more than 140 selected distribution partners in 120 countries, L&R is represented in all important markets around the world and was able to realize a sales volume of 793 million euros in 2023. The company’s headquarters are located at the Rengsdorf (Germany) and Vienna (Austria) sites.
The entrepreneurial spirit of L&R is reflected in the corporate claim: People.Health.Care. – the human, the health and the care for both.
Problem
Lohmann & Rauscher, a leading manufacturer of medical devices and hygiene products, produces some of its high-quality products at the Schönau an der Triesting site. However, two areas in the production process were identified where targeted optimisation could help to further streamline the production process.
First, there was potential for improvement in the notification system for technical faults. If a machine required maintenance or repair, it could take some time before the relevant contacts were informed. Faster information transfer would help to ensure that potential downtime could be rectified more efficiently and that production time is utilised as effectively as possible.
Second, there was a lack of visibility on when a machine had completed a task. Here, too, there was room for improvement.
Solution
Lohmann & Rauscher implemented the safeREACH emergency alerting system in order to organise production processes more efficiently and to shorten response times in the event of technical faults. With this system, employees can immediately alert the relevant people via the user-friendly safeREACH cockpit with only one click. Feedback can be given directly using the chat. Depending on the type of incident, an alarm or information message is sent to the relevant contact person, minimising delays and significantly speeding up processes.
Initially, there were doubts about whether employees would accept the digital innovation. However, the safeREACH system impressed them with its intuitive operation and reliability. It quickly became clear that it offers a practical and easy-to-use solution that makes work easier for everyone involved. The introduction of the safeREACH alerting system was ultimately accepted by all employees.
Why did you look for a rapid alerting tool?
We looked for a rapid alerting tool because it was important to us to further reduce non-value-adding activities and to make our processes even more efficient. One major goal was to minimise machine downtime following a malfunction. By directly alerting the responsible employees, we can now react much faster to technical problems. We also wanted to minimise the unnecessary time employees spend going to machines to perform checks. This allows our staff to devote more time to value-adding tasks.
Where do you see the advantages of safeREACH?
Primarily, we see the advantages of safeREACH in the flexibility, efficiency and user-friendliness of the system. With safeREACH, we can ensure that we are available at all times and can react immediately to technical faults, thereby minimising downtime. The easy-to-understand admin interface is another major advantage, as we can customise it quickly and flexibly to meet our needs.
In addition, safeREACH provides us with detailed reports that allow us to pinpoint specifically when and where faults occur, enabling us to continuously improve our processes. Thanks to the ease of use, we quickly arrive at an effective solution, which greatly increases acceptance within the team and ensures smooth integration.
For which use cases do you use safeREACH?
We use safeREACH primarily for two key use cases: firstly, for rapid alerts in the event of technical faults and, second, for transmitting information on completed machine orders. In the event of a technical malfunction, safeREACH enables us to notify the responsible employees immediately so that problems can be rectified as quickly as possible.
The system triggers targeted alarms as soon as a machine breaks down, which helps us to avoid unnecessary downtime. We also use safeREACH to notify the team when a specific job on a machine has been completed. Everyone is therefore kept up to date at all times, and we can proceed without delay.
Which features do you find particularly helpful?
We find the one-time link for the cockpit, which allows employees to trigger and stop alarms quickly and from anywhere, particularly helpful. This makes it very flexible for us to use and significantly simplifies our day-to-day work. No familiarisation or training is required, and no major configuration effort is needed.
The option of deputy, group and cascade alerting is also a big plus for us, as it enables notifications to be sent to different areas and employees.
We also appreciate the differentiation between alarms and information messages: urgent messages can be sent as alarms, which are hard to miss, while less urgent messages can be sent as info messages. This keeps communication clear and focused.
How do you feel about working with safeREACH?
The collaboration with safeREACH is very smooth and efficient. We particularly appreciate the fast response times and the friendly relationship with the team, who are always ready to help with any questions or adjustments in a clear and straightforward manner. Overall, we feel that we are in very good hands thanks to the reliable support we receive.
If you had to describe safeREACH in three words, what would come to mind?
Flexible. Intuitive. Works.