PDCA cycle
The PDCA cycle, also known as the Deming cycle, is a systematic method for the continuous improvement of processes and products. Originally developed by Dr William Edwards Deming, a pioneer in the field of quality management, the PDCA cycle has become established in many industries, including crisis management.
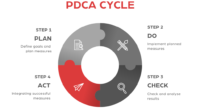
1.666 alarms per second
safeREACH as your powerful emergency notification system with up to 100.000 alarms per minute. Successfully used by multinational corporations, medium-sized companies and public authorities. ISO-certified server infrastructure.
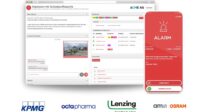
Origin and concept of the PDCA cycle
The PDCA cycle was popularised by Deming in the 1950s, based on the ideas of Walter A. Shewhart. Shewhart developed the concept of the “Plan-Do-Check-Act” cycle (i.e. the PDCA cycle) to improve the quality of production processes. Deming spread this methodology worldwide, particularly in Japan, where it contributed significantly to the economic upturn after the Second World War. The spread of Deming also gave rise to the name Deming cycle.
4 phases of the PDCA cycle
- Plan: In this phase, goals are defined and measures are planned to achieve these goals. This includes identifying problems, analysing data and developing hypotheses to solve these problems.
- Do: The planned measures are implemented. This is a test phase in which small, controlled changes are made to test the hypotheses.
- Check: The results of the implemented measures are measured and analysed. It is checked whether the measures have brought about the desired improvements.
- Act: Based on the results of the check, successful measures are standardised and integrated into the regular process. If the measures have not achieved the desired results, the cycle is repeated until the problems are solved.
Over 20 years of experience in alerting
IT alerting, fire alarms, alerting company first responders and much more. ISO-certified server infrastructure. Used by SMEs, corporations, authorities and public organisations.
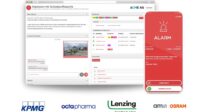
Relevance of the PDCA cycle in crisis management
The application of the PDCA cycle in crisis management offers several advantages:
- Systematic approach: The PDCA cycle provides a clear structure for the continuous improvement of emergency plans and processes. This helps to identify systematic weaknesses and rectify them in a targeted manner.
- Flexibility and adaptability: Due to the iterative nature of the PDCA cycle, companies can continuously adapt their emergency strategies to new threats and changes in the environment. This is particularly important in a dynamic threat landscape, such as cyber attacks or geopolitical tensions.
- Promoting resilience: The PDCA cycle helps organisations to become more resilient by learning to recover quickly and effectively from crises. This not only strengthens operational continuity, but also the trust of customers, partners and employees.
- Increasing security: By regularly reviewing and updating emergency plans, companies ensure that their security measures are always up-to-date and work effectively.
Legal frameworks, i.e. the NIS-2 directive, play an important role in the protection of critical infrastructures. These regulations also promote the application of the PDCA cycle by setting requirements for risk assessment, the implementation of protective measures and the continuous improvement of resilience.
1.666 alarms per second
safeREACH as your powerful emergency notification system with up to 100.000 alarms per minute. Successfully used by multinational corporations, medium-sized companies and public authorities. ISO-certified server infrastructure.
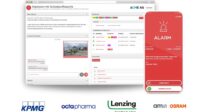
PDCA cycle as an important management tool
The PDCA cycle is a proven tool for the continuous improvement and adaptation of plans and processes. Thanks to its systematic and iterative approach, it can also help companies in crisis management to strengthen their resilience and prepare effectively for crisis situations. The PDCA cycle is an important tool for companies that want to continuously improve their management skills.
Another method that is often used in emergency and crisis management is the FORDEC method. You can find more information on the linked page.